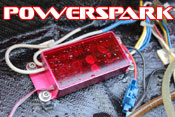
We Build an Ignition System...
Most conventional 2-cylinder-engines based on the ZENOAH, CHUNG-YANG, RCMK occupy a considerable amount of space because of their width or height. This is mainly due to the two red primary ignition coils or other ignition coils. The final width or height depends on how the coils are arranged. On all “real” 2-cylinder engines the coils are typically installed on the sides, either diagonally or horizontally. 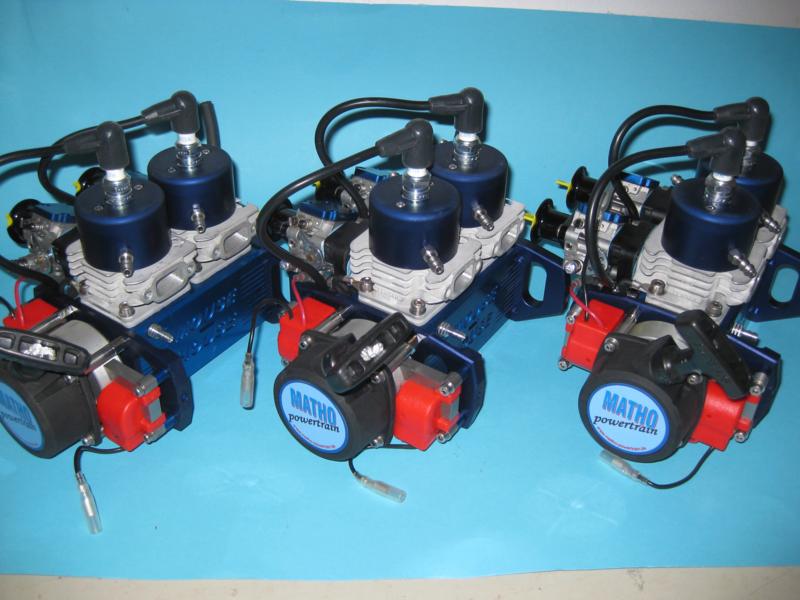
For example: a 2-cylinder engine MOUSE HOUSE with a standard ZENOAH CDI magnetic ignition. One exception is the “Heilbronner-Bub” (this engine I do not consider as a 2-cylinder since it is a coupled engine… without putting its usefulness into question), this engine is built both narrower and longer.
The width of the 2-cylinder engines (and also our 3- and 4 cylinder engines) often makes the installation of cats impossible, as there is often not enough space in the skids. And even in monos there is less space left when two engines are arranged side-by-side. A superior solution is needed and this better solution is the “electronic ignition”.
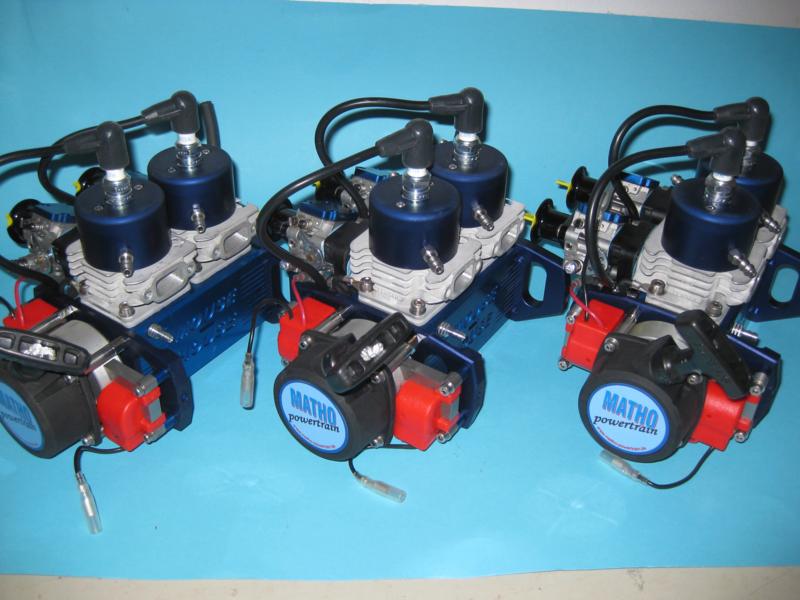
For example: a 2-cylinder engine MOUSE HOUSE with a standard ZENOAH CDI magnetic ignition. One exception is the “Heilbronner-Bub” (this engine I do not consider as a 2-cylinder since it is a coupled engine… without putting its usefulness into question), this engine is built both narrower and longer.
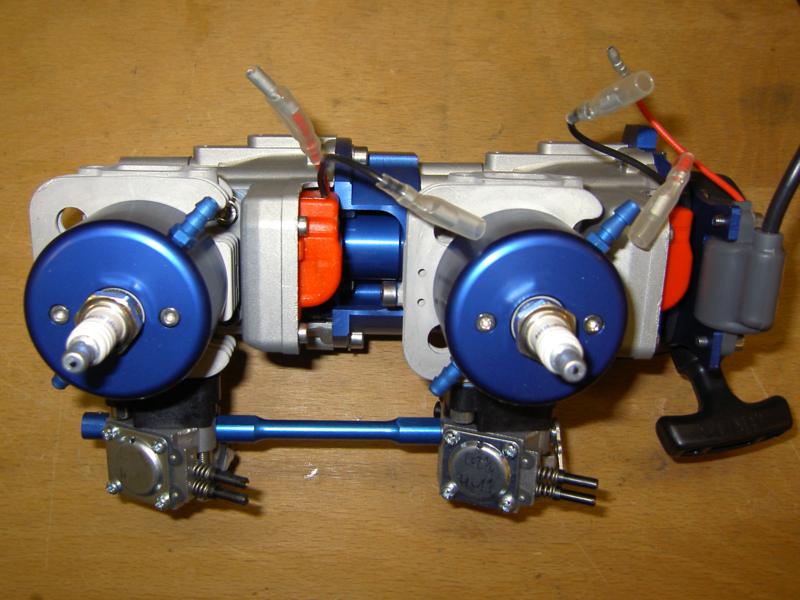
Solution: Electronic Ignition
There are several commercial electronic ignitions obtainable on the market. Personally, I was not attracted to the presented solutions since they do not fully exploit the possibilities of the engine. In addition a monitoring of the receiver system is not implemented and I am not aware of any commercial systems that have adjustable ignition maps, which are programmable by the user without requiring a computer. The known commercially available ignitions do not have a display and therefore they do not display engine speed information, although the electronics does measure such data.
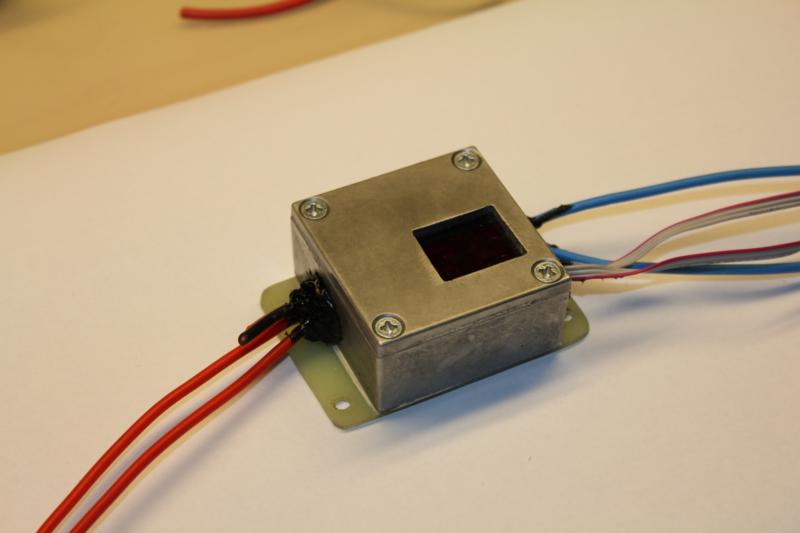
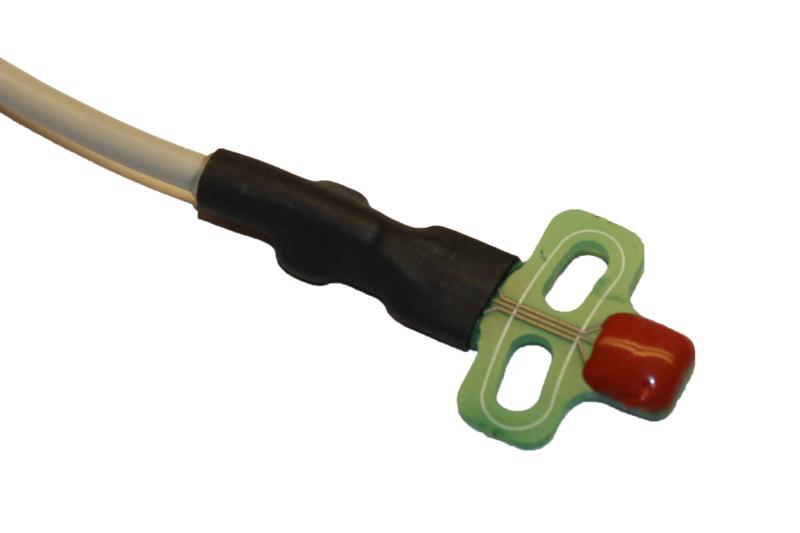
In the case of this project I was able to convince experienced electrical engineers from the automotive industry, who were willing to develop an ignition system to a typical automotive standard. This expert group is organized under the name “tne-systeme UG limited” and has the capability to produce the advanced ignition system in volume.
The book of requirements

- several pre-programmed ignition maps that the customer can select using a menu (no computer or laptop required)
- customer is able to program his own ignition maps
- integrated engine speed counter with display of current speed or maximum speed (like “Sendec”), exception values (jump of the boat with short period of over speed) has to be filtered
- RC servo signal monitoring with shutdown of engine when receiving invalid signals
- RC main battery monitoring with warning by means of engine splutter at a specified low voltage and shutdown of engine when battery failure occurs (voltage thresholds can be adjusted)
- kill switch function
- waterproof sealing
- interference is not allowed to impact the RC-system
- small sensor with magnet control (see installation width)
- engine speeds up to 30000 rpm (applicable for converted glow engines)
- capable of firing up to 4 cylinders
This leads to the conclusion, that the ignition voltage should not be generated in the ignition system itself but rather with the standard gray secondary coils from ZENOAH or RCMK. Hence, they remain in the system but do not have to be assembled directly to the engine.
Short sidestep: The development in the automotive industry is done in several stages.
XP: eXperimentation Phase (is the concept suitable to be developed for series? Parts are produced and assembled experimentally, in very small quantities.)
AP: Application Phase (does the system work in conjunction with the periphery? Some parts are already series level, small quantities, parts are partially produced on prototype machines.)
CP: Confirmation Phase (does the system function with production parts under production conditions and all possible states?)
XP: The Experimentation Phase
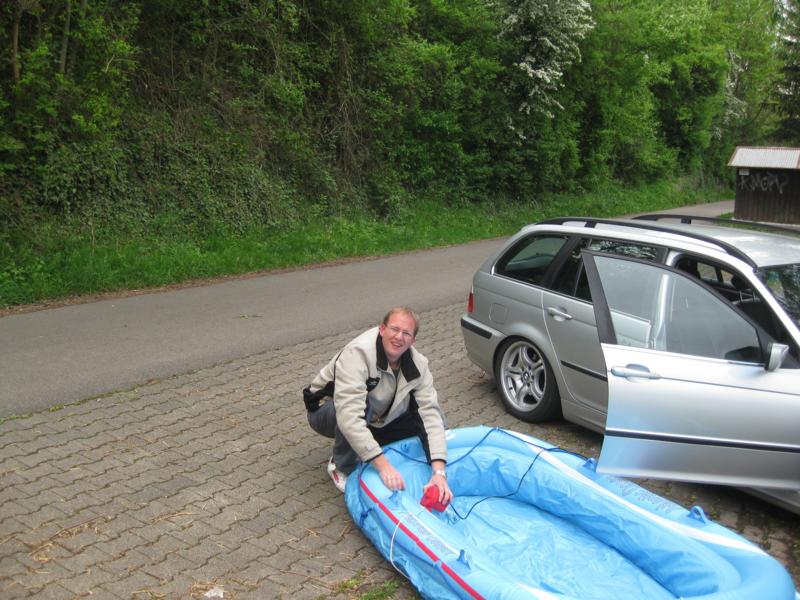
Here we tested the basic functions, usually in dry conditions with a running engine. The first endurance tests were performed on an engine test rig. The tests were performed on water, supported by our saving boater Daniel “Seewolf”.
![]() |
![]() |
![]() |
Ignition system |
Included in 1- and 2 cylinder version |
NoMercy with BEE HOUSE engine and POWER SPARK ignition system |
However, we always had dropouts after 50 m. Until we finally established the cause i.e. from an old FUTABA 1024PCM. This proved that the ignition stops the engine reliably, as soon as no reliable receiver signal is detected or disrupted. After the conversion of the system to 2.4 GHz with CORONA- components everything worked properly and reliably. Later we realized that the 40 MHz-module is suffering from old age, according to a web-blog, I was not the only person with a similar problem.
AP: The Application Phase
The housing was assembled from aluminum profiles. However, the circuit board is already produced in series quality. In this phase we fixed the 10 prior programmed ignition maps and wrote the 54-page manual that describes all functions in detail. The various safety shutdown functions were tested under practical conditions and thus validated.
Furthermore, the software was developed in the application phase. For example: How should the RC-supervision be implemented in detail (parameter)? How does the engine-stuttering work in the water? What are high-quality values for the ignition maps (pre-ignition angle depending on engine speed)?
![]() |
![]() |
![]() |
assembly kit 1 |
assembly kit 2 |
assembly kit 3 |
CP: The Confirmation phase
On April 2010 we started the CP: The housing was machined from solid and red anodized. The red Plexiglas cover was machined fitted with special glue. The other parts were already from standard production. Even in this phase we optimized the values of the ignition maps and did some fine tuning on various functions. The unit was sent to an EMC-laboratory to obtain the “CE”-mark.
The first engines were equipped with the ignition system and distributed to a few sample customers for testing.
The ignition systems are adapted to all 260 ZENOAH and the similar derivates (for example RCMK and Chung Yang) with an assembly kit that I offer on my homepage www.matho-powertrain.de
The ignition has its own homepage: www.power-spark.de
The POWER SPARK ignition system consists of the following components:
• ignition box with all necessary cables and connector for sensor module
• sensor module with cable and connector
• programming magnet in red shrink hose
• fuse with fuse folder
• operating manual
The POWER SPARK is available in the following versions:
• 1-cylinder with or without RC-monitoring features
• 2-cylinder with or without RC-monitoring features
• 4-cylinders (double-twin) / (double-boxer) with or without RC-monitoring features
• the 4-cylinder-versions can also be used for my 3-cylinder engine, since it’s a “one and a-half-twin” concept.
The assembly kit for ZENOAH or RCMK consists of:
• flywheel aluminum (kit 1 & kit3) or brass (kit 2) with assembled magnet for speed sensor
• sensor bracket (silver or black)
• spaces for sensor bracket (silver or black)
• Special versions for rear exhaust engines for racing (FSR-x use).
![]() |
![]() |
POWER SPARK ignition: 1- and 2-cylinder versions |
POWER SPARK ignition: 3-and 4-cylinder versions |
![]() |
![]() |
MOUSE HOUSE with brass flywheel and sensor (cp) |
Waterproof POWER SPARK system |
Easy Operation
The installation of the ignition system is in our view self-explanatory.
The start-up is quite simple:
If no RC-monitoring is desired, then simply power the ignition and start the engine. If everything is connected correctly, the engine starts - due to the more powerful spark- no later than 3 times.
Practical experience:
The original ZENOAH engine (tuned slightly) in my NoMercy turned about 500 rpm higher than the standard magneto ignition (load condition). Reason: the ignition spark is more powerful. Hence, the combustion at high speeds is enhanced. For the 3- and 4-cylinder engines it looks even better: with the magneto ignition the energy of the red primary ignition coil had to be distributed to the two grey secondary coils, resulting in a weaker spark. Now, the motors can finally show their full potential.
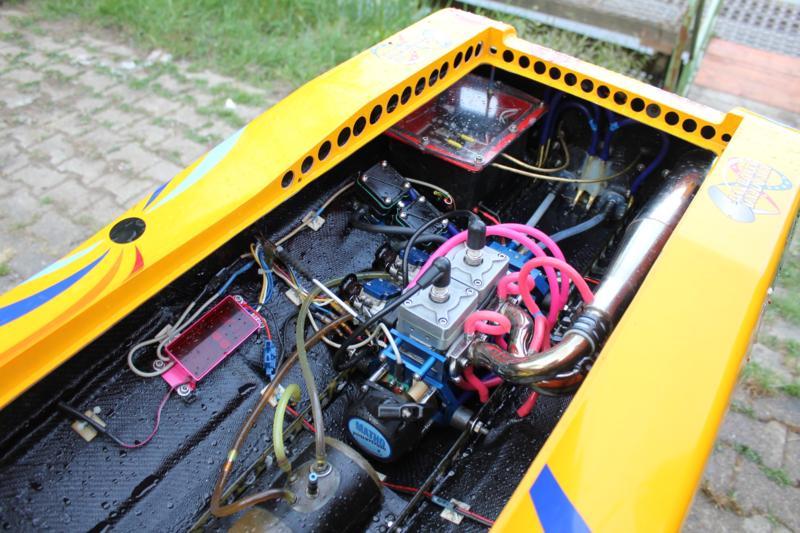
Currently, we are building a 30 kg Mono with our RAT HOUSE and the POWER SPARK ignition, when we are finished, we look forward to reporting back our results.
What works very well is the splutter function that is activated when the battery voltage is low. Even in the fray, if several boats whisk the water the same time, one can see very well that the rooster tail interrupts shortly and then resumes. Below the selected stutter speed (in my case 11000 rpm) the engine operates as normal, so one can ride to shore normally.
Right now we have finished adding more function to the ignition system:
- Speed dependent output for pump, throttle, signal etc.
- Switching output (flashing or non-flashing) to signal engine stop (blink a LED)
- operating time counter
- alternating display of battery voltage and maximum achieved engine speed automatically after engine stop (adjustable)
For more information visit our webpage at:
www.POWER-SPARK.de
and
www.MATHO-powertrain.de