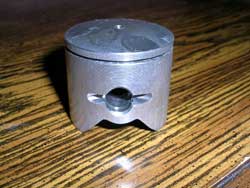
Does the top diameter of my
piston need to be machined in my engine?
Well I have been asked this question so many times that I figured it was worth some time answering it with a write up. The simple answer is yes, the explanation why is not quite as simple, but I will try to explain the best that I can from some of the knowledge that I have learned over the years.
This simple modification is done on a lathe
by removing .002 to .003 from the outside diameter of the piston starting at
the
The true culprit of our problem is heat
expansion on the crown area of our piston. With the addition of tuned pipes and
the recent wave of modifications to the piston to make it lighter has only made
the problem worse. The crown of the piston with heat expansion will grow more
than the rest of the piston even in stock form and there is no simple way to
cure this problem. When engine tuners remove material from the inside of the
piston area to make the piston lighter it actually makes the problem worse as
you have less aluminum to absorb and disperse the heat from the combustion
cycle. Some would believe that if it
CC Racing Engines
www.cc-racingengines.com
Editor Note: Here is a short article on how I made a fixture for the piston to turn it in a lathe. M.L. CLICK HERE to go to article .